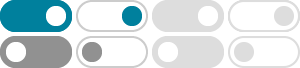
(PDF) Design and Control of a Hydraulic Hexapod Robot
Apr 25, 2022 · This paper focuses on the system design and control strategies of a hydraulic hexapod robot (HHR) ZJUHEX01 with a two-stage supply pressure hydraulic system (TSS).
Hexapods & Positioning Systems - Moog Inc.
Moog’s 6-axis hexapods, also known as Stewart platforms, are parallel kinematic robotic systems capable of positioning or moving a payload in all six degrees of freedom (6-DOF): lateral, …
- [PDF]
HEXAPODS - Moog Inc.
A hexapod is a robotic manipulator capable of moving a payload in all six degrees of freedom: lateral, longitudinal, and vertical translations as well as roll, pitch, and yaw rotations. Motions …
Design and Control of a Hydraulic Hexapod Robot with a Two …
Apr 25, 2022 · With the help of hydraulic actuation, hydraulic hexapod robots (HHR) can provide large force output, as well as high power density and strong robustness, which is suitable for …
Motion planning and simulation verification of a hydraulic hexapod ...
Oct 15, 2015 · This paper proposes a low energy cost foot trajectory planning method to realize a constant velocity of the body and optimize the power and flow consumption of a hexapod …
Mechanical Design and Gait Optimization of Hydraulic Hexapod …
This paper presents a structural optimization method of the hydraulic walking robot by optimizing its mechanical structure and gait parameters simultaneously. The mathematical model of the …
Parallel-kinematic design for six degrees of freedom making it significantly more compact and stiff than serial-kinematic systems, higher dynamic range, no moved cables: Higher reliability, …
Control of a hydraulic hexapod for a Hardware-in-the-Loop axle …
May 28, 2016 · The present paper describes the controller design for a hydraulic hexapod which is used as an excitation unit for a Hardware-in-the-Loop axle test rig. This includes a …
This work focuses on the mechanical design and gait optimization of a hydraulic hexapod robot to reduce energy consumption.
Hydraulic hexapod simulation table expands frequency range up to 100 Hz, increasing the speed, range and flexibility of automotive component testing.